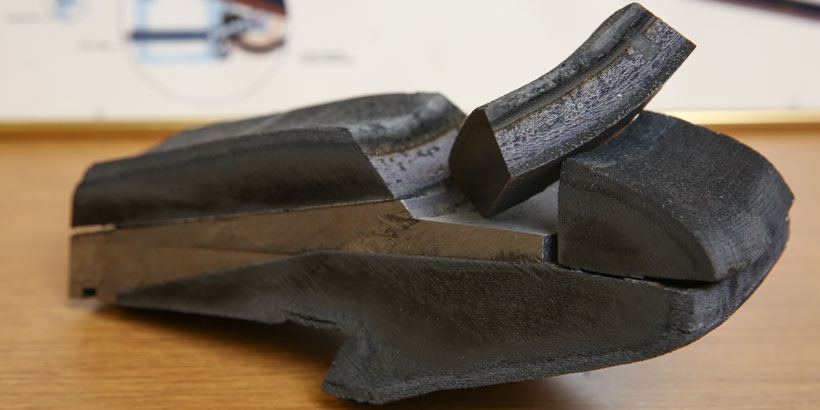
HUNTSVILLE, Alabama – A professor at the University of Alabama in Huntsville is pioneering a new technology that could provide a more environmentally friendly path to explore space.
William Kaukler, an associate research professor at UAH’s Rotorcraft Systems Engineering and Simulation Center, has been awarded a patent for a green process he developed that produces the carbon fiber used in ablative rocket nozzles and heat shields.
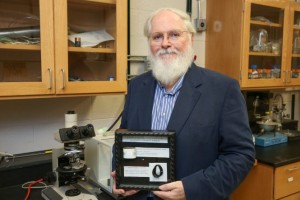
Kaukler’s work could interest NASA, which has a dwindling supply of cellulose rayon fiber, after the old way to manufacture it ceased in the 1990s due to hazardous byproducts.
The production process developed by Kaukler recycles all the byproducts. It also uses ionic liquids.
“Other people know about using ionic processes to make fibers but they are not making carbon fibers with them,” Kaukler said.
The trick, he continued, was to make the properties of this fiber match the properties of the fiber made by North American Rayon Corp., which ceased rayon production in the U.S. after it couldn’t afford to comply with Environmental Protection Agency regulations for the hazardous byproducts.
MAKING ROCKET NOZZLES
The carbon fiber used to form a solid fuel rocket nozzle is not the same as those used to make aircraft or car parts, Kaukler said. The only way to make carbon fiber suitable for rocket nozzles is to start with cellulosic fiber.
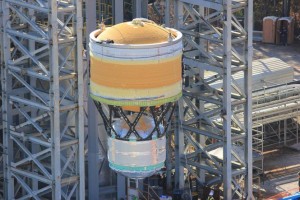
Specifically, Kaukler’s process could help NASA produce the solid rocket motors in the next-generation Space Launch System, the space agency’s most powerful rocket, now being prepared for structural testing at Marshall Space Flight Center.
Additionally, Kaukler’s method could help make heat shields used in re-entry to Earth’s atmosphere or on planetary probes designed for landing,
Rocket nozzles of Army missiles also incorporate the same carbon fiber.
Kaukler, a materials scientist who has been a NASA contractor for 35 years, said the idea for the new, green process came about five or six years ago. He developed it at UAH’s Reliability and Failure Analysis Laboratory, with funding from the U.S. Army’s Aviation and Missile Research Development and Engineering Center, located at Redstone Arsenal in Huntsville.
“The patent is mostly about how to process the ionic liquid cellulosic fiber into carbon fiber suitable for making rocket nozzles and heat shields,” he said. “The next step is going for a second patent with revisions and improvements on the first one.
“The application on the first one was put in two years ago. I only just got it now, and I’ve learned more since then.”
Beyond that, Kaukler said the goal is to figure out a way to scale up the process so that a NASA contractor would find it a viable option.
“The real issue is scaling everything up,” Kaukler continued. “Ionic liquid is expensive, and on a small scale, it’s not a profitable process. If you want to stay profitable, you have to recover 99 percent of the ionic liquid.”